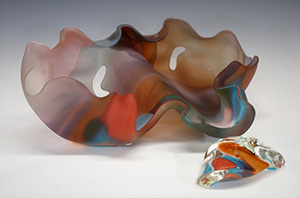
Though the history of glassblowing stretches back to the middle of the 1st century BC, the last six decades have seen the practice of blowing glass for artistic purposes evolve hugely. The world of handblown art glass has advanced significantly since the start of the studio glass movement in the early 1960s. Harvey Littleton is cited with kick-starting the practice of adding small furnaces to studios and paved the way for artists like Dale Chihuly and Marvin Lipofsky to cement their place in art history.
Features of handblown art glass
One of the key features of handblown glass pieces is that they have small bubbles and other irregularities that make them unique. Pressed factory made glass does not have these pecuniary qualities. Learning how to blow glass can take many years. It is a very valuable skill and it can take a great deal of patience and time to master the technique. In ancient times, glass blowers were kept on Islands to make sure their secret glass handblowing knowledge was not disseminated.
Millennia of history
Blown glass was apparently first introduced in Syria. The Syrians found they could put a bowl of molten glass into a tube then blow into it. The technique was taken up by the Romans and the popularity of handblown art glass spread across Europe before hitting America in the early 17th century. With the passing of time, blown glass became more affordable and was soon being used for everyday items. Blown glass also played a big role in the Art Nouveau movement and enjoyed a big resurgence in the 1960s.
Those who wish to create their own blown glass pieces need to invest money in the equipment to do so. They need to obtain silicon dioxide, which is also known as silica or sand. This must be mixed with various minerals and components. To lower the melting point and make silicon dioxide easier to work with, sodium dioxide and calcium oxide can be used. Other materials that might be added to the mix include barium oxide, aluminum oxide and zinc oxide.
Colouring glass
Glass can be coloured using a number of materials. Copper and silver are often used in the colouring process, and gold chloride can turn the glass dark red. Chromium can make it go green. Glassblowers must obtain a blowpipe to get started. The blower can push air into the glass at one end and dip the other in molten glass mixture. Furnaces and other tools are normally used.
Offhand blowing is the main process for making handblown art glass. The majority of the work involves the hand, though some other tools may play a small role. Furnaces usually need to reach a temperature of above 2000 degrees Fahrenheit so raw materials can be transformed into molten glass. When the piece of blown glass is the right size, tools may be used to create the desired shape. The piece may be placed in a mold before blowing commences. Once the right shape is in place, the glass is taken to the third and final furnace known as the annealer, which brings the temperature down and prevents it from breaking. Cooling times can vary and can be determined by how complex the piece is.
Limitless possibilities
The amount of skill and creativity that goes into creating handblown art glass means it’s no surprise to see the best pieces sell for so much. Lovers of these products adore features like their tiny bubbles as well as the fact that each piece is completely unique. They also love the seemingly infinite range of designs, shapes and colours that are available to them. Many art glass pieces produced using these methods feature a whole array of different colours working together to create something truly beautiful and unique. There are two main methods used to create blown glass, which are offhand glass blowing and lampworking. Lampworking is normally used to produce items featuring premade glass. Hand blown art glass pieces can be very collectable, and connoiseurs of these pieces tend to source items from all across the world.